According to a recent paper entitled “Design and testing of a dual-channel non-dispersive infrared CO2 gas sensor”, published in the journal China Laser by Professor Tan Qiulin’s team at North Central University, a miniature dual-channel non-dispersive infrared (NDIR) CO2 gas sensor has been designed and implemented, using the standard In this paper, a miniature dual-channel non-dispersive infrared (NDIR) CO2 gas sensor is designed and implemented, using the standard gas concentration calibration method to achieve temperature compensation of the sensor, enabling it to measure accurately at different temperatures and concentrations.
Gas sensors based on the infrared absorption principle have the outstanding advantage of high selectivity, but face problems such as low integration, large size, low accuracy and dependence on imported core components. Currently, imported sensors are commonly used in China, or semi-finished products are purchased for secondary processing. In recent years, with the efforts of major research institutions and universities, the domestic independent design of infrared sensors is developing at a rapid pace, but there are problems of poor sensor sensitivity and small range.
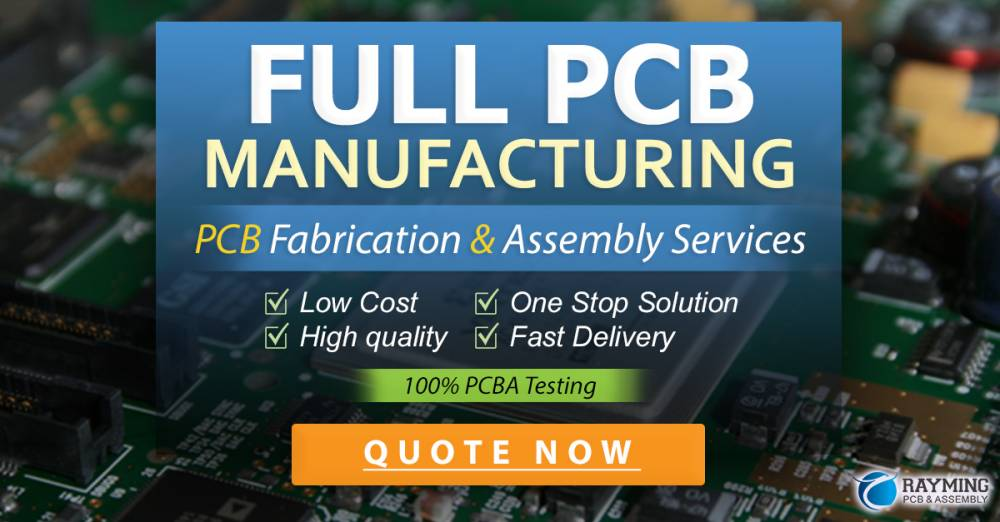
Based on this, this paper proposes a miniaturised non-spectroscopic infrared CO2 sensor based on the infrared pyroelectric effect, based on a dual-band single gas path design. Using the calibration method, a temperature compensation method is explored to measure the output value of the detector at different concentrations and temperatures, and a relationship model between temperature, CO2 concentration and detector output value is established to realise the temperature compensation of the sensor so that it can make accurate measurements at different temperatures and different concentrations.
Overall design of the infrared CO2 sensor
The infrared CO2 sensor designed in this paper consists of four main parts: the infrared light source, the gas chamber, the infrared detector and the main circuit system, as shown in Figure 1.
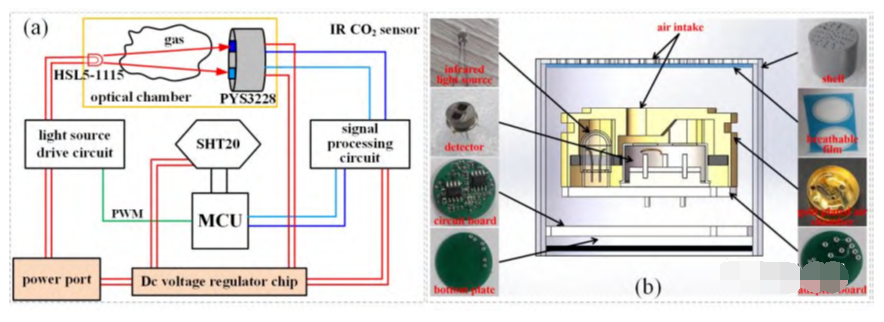
The size and performance of an infrared CO2 sensor is largely determined by its optical gas chamber. In order to miniaturise the sensor while maintaining high performance, this paper designs a C-type multi-reflective gas chamber structure, which increases the light range and ensures the length of the light-gas interaction, and integrates the light emission, light propagation and absorption, photoelectric signal conversion and signal processing modules to obtain a miniaturised gas chamber with a height of 8 mm and a diameter of 18 mm. This minimises the size of the sensor. The result is a miniature infrared CO2 gas sensor with a diameter of 23mm and a height of 10mm.
The infrared light source HSL5-115 was chosen to provide the required wavelengths in the infrared band. The infrared detector is the PYS3228 detector, which consists of two channels, one with a 4.26μm band filter placed in front of it as an operating window for absorption near 4.26μm, and the other with a 3.9μm band filter placed in front of it as a reference window for absorption near 3.9μm.
The use of a single optical path dual wavelength differential design ideas, can effectively eliminate the interference of the gas chamber and light source and impurities, reduce the ambient temperature, dust, moisture and other interference factors on the system, so as to reduce the measurement error, improve the system measurement accuracy. The workflow of the system is as follows: firstly, the microcontroller outputs a reasonable frequency of light source driving signal to light up the infrared light source HSL5-115, the infrared radiation from the infrared light source is absorbed by the gas in the gas chamber, and then the infrared radiation in the 4.26μm band and 3.9μm band through the front filter of the PYS3228 detector is irradiated to the sensitive element to produce an electrical signal, which is processed and filtered, and then input to the The electrical signal is processed and filtered, then fed into the ADC in the microcontroller and processed with the temperature information to calculate and output the CO2 gas concentration in the gas chamber.
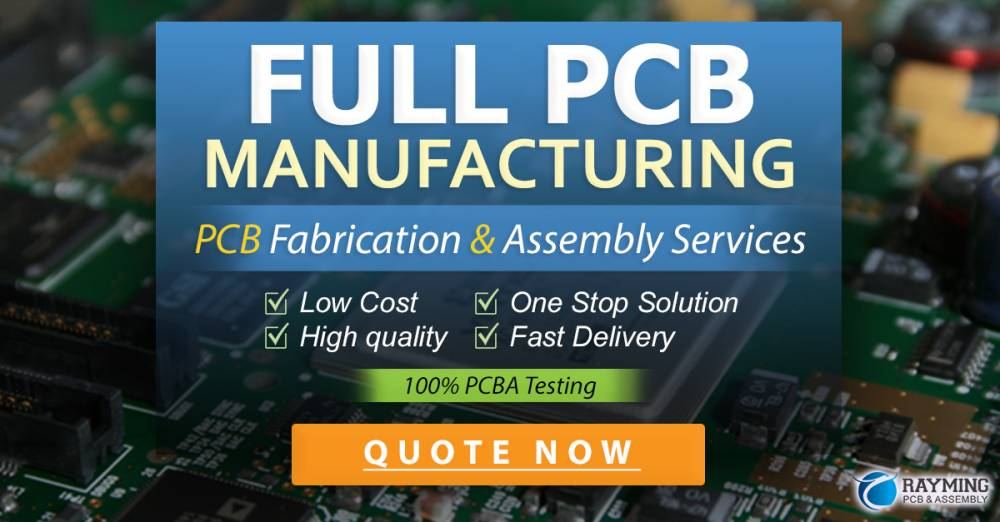
Hardware circuitry and software programming
The infrared CO2 sensor hardware circuit and software program are designed in a modular way to reduce system coupling. The hardware mainly consists of the light source driver circuit, signal processing circuit design, etc. The software consists of the light source driver, the temperature and humidity acquisition program and the data processing program, etc. The upper computer is written to display the gas content information and the ambient temperature information in real time.
The measurement of gas concentration has a strong influence on the measurement of gas concentration due to the interference with the ambient temperature during the test. Therefore, the use of temperature compensation ensures the accuracy of the measurement results. The ambient temperature acquisition circuit uses a temperature and humidity chip SHT20. The temperature values collected by the temperature and humidity sensors are read by the microcontroller as the host computer via IIC communication and are compensated for by software within the microcontroller.
Sensor test calibration and analysis
In order to ensure the accuracy and detection range of the sensor, a standard gas concentration calibration method is used to calibrate the sensor. A sensor calibration experiment platform was built, as shown in Figure 2, consisting of a high and low temperature humidity chamber, a standard gas source and sensor tooling. The results of the calibration are shown in Figure 3.
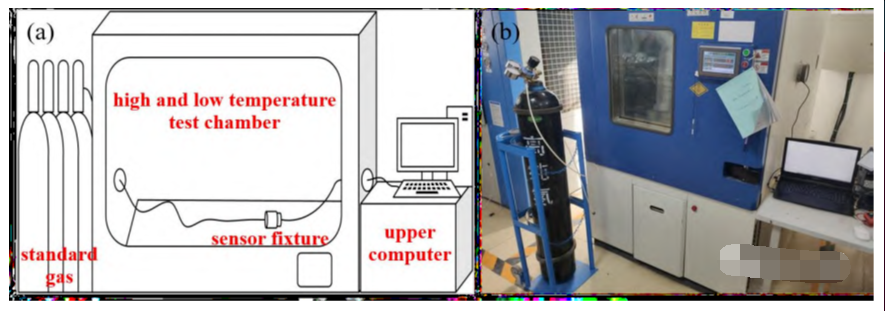

From Figure 3 it can be observed that the temperature (t) affects the peak-to-peak difference (d1) and hence the output gas concentration, and it can be noted that the temperature affects the peak-to-peak difference approximately linearly. Fitting the temperature to the peak-to-peak difference (d1) gives the equation used to calculate the compensated difference (d) versus temperature (t) and peak-to-peak difference (d1) and gives a plot of the compensated difference (d) versus the standard gas concentration (C), as shown in Figure 4.
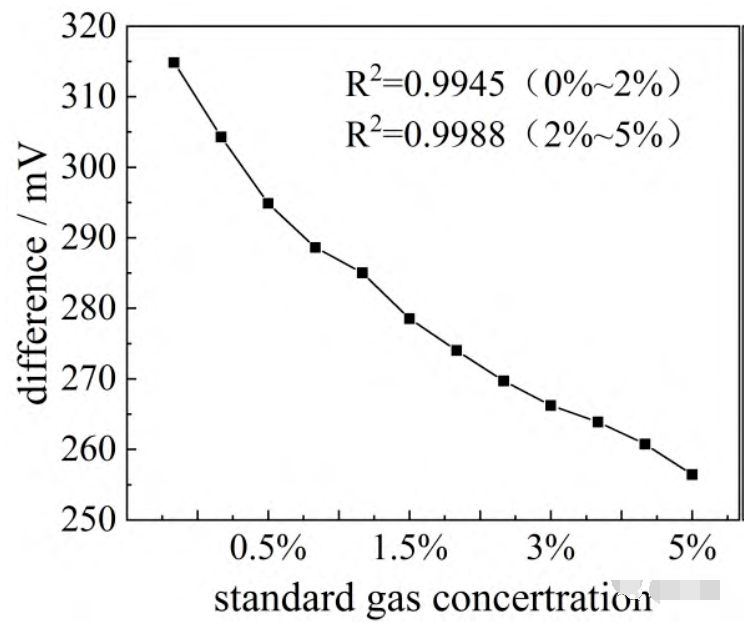
Conclusion
CO2 sensors have a very important role in industrial production, life and medical diagnosis. In this paper, a miniature non-spectroscopic infrared CO2 sensor based on the infrared absorption spectroscopy principle is designed and implemented using a single gas path and dual wavelength differential method. Using the standard gas concentration calibration sensor method, the temperature compensation of the sensor is achieved, enabling accurate measurements at different temperatures and concentrations. The sensor achieves a miniature design of 23mm in diameter and 10mm in height, with an error value of less than 0.1% at 0% to 2% concentration and less than 0.25% at 2% to 5% concentration for accurate measurement. It can provide core devices and technical support for the monitoring of CO2 concentration in China’s industrial manufacturing and production environment, which is of great practical significance to ensure safe production and human health.