In modern, highly automated factories, inductive position sensors are replacing Hall-effect position sensors and older magnetic resolver solutions as the ideal choice for motor control designs as the demand for high accuracy, high efficiency and low cost continues to grow. And because inductive products are also easier to integrate into simple, compact printed circuit boards (PCBs), they can further meet the need for lighter, smaller and lower costs.
In this article, Renesas Electronics brings you an inductive absolute position sensor solution that is not only simple but also very cost effective as it is constructed from off-the-shelf devices (i.e. a standard PCB, a Renesas position sensor, some simple passive components and a piece of metal to act on the sensing target) and can support up to 250, 000RPM.

The solution uses dual IPS2200 inductive position sensors (IPS) for absolute position detection, optimising the coil size, and the module packaging is in line with mainstream market trends for 35mm motor designs, which increases the universality of the solution. accuracy, while accommodating off-axis (through-axis and side-axis) and shaft-end arrangements. Compared to conventional resolvers, the magnet-free IPS2200 is up to a tenth thinner and a hundredth lighter than conventional resolvers, and has an electrical speed of up to 250 krpm.
Thanks to the sensor’s slim profile and full stray field immunity it makes motor integration easier and provides customers with the standard materials needed to manufacture their own resolver alternatives, further reducing BOM costs. The IPS2200 achieves up to 10 times the speed and very low latency with a four or six wire connection compared to a resolver or magnetic based solution.
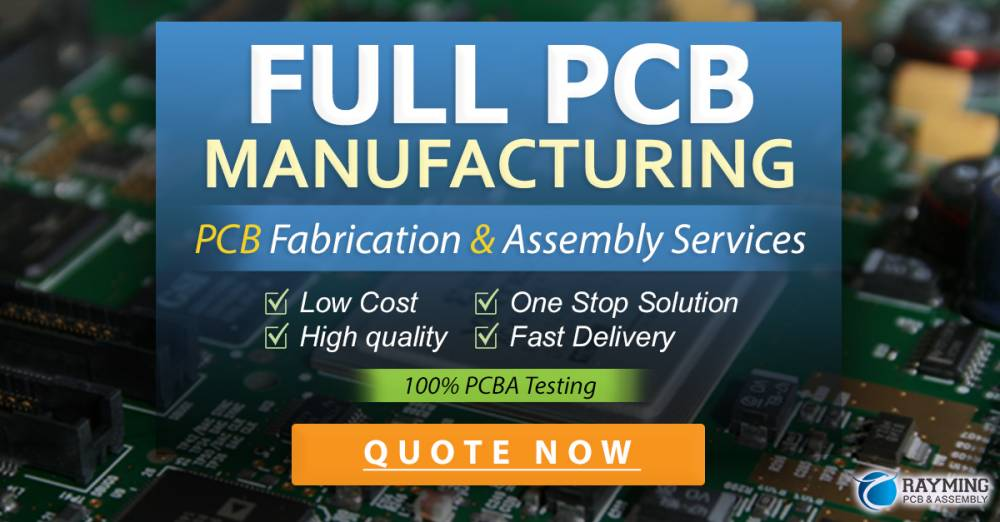
The layout of this solution is designed so that the position sensing element is not inside the Renesas Electronics IC, but rather a set of coils on the PCB. The advantage of this layout is that the sensors can be customised and designed as a system to suit the customer’s application scenario.
In terms of MCU selection, the solution uses a 32-bit MCU with an on-chip floating point unit (FPU), the RX24T, which can operate at up to 80MHz in normal operation. The MCU is suitable for dual inverter control, can drive two motors simultaneously and can efficiently compile complex inverter control algorithms.
The RAA214250 low dropout linear regulator is also used in the solution, with an operating voltage range of 2.5V to 20V, an output current of up to 500mA and a typical dropout voltage of 269mV. The output voltage can be adjusted from 1.224V to 18V using an external feedback resistor.
With the above device characteristics, this solution offers several system advantages:
- Cost-effective and supports faster speeds (up to 250,000RPM).
2. The solution can be designed to suit customer application scenarios as it supports three mechanical types and the number of motor electrode pairs is matched to the number of sensor sectors.
3. This MCU has three ADC units with dedicated channel sample hold. the AD conversion can be initiated via a synchronous trigger.
4. High precision, actual resolution: 15 bits, accuracy: 12 bits.
Can be applied to:
- BLDC rotor position detection and inspection; suitable for any electrode pair number.
2. Replacement for brushless resolver.
3.Magnetless rotor speed sensor.
Motor control plays a very important role in industrial automation, for which Renesas Electronics has introduced a variety of successful product portfolio solutions dedicated to helping customers achieve accurate, efficient and low power consumption motor designs.