Control requirements and control principle
Automatic control of the water tower, that is, in the case of unmanned operation, the water supply system in the water tower water level below a certain lower limit position, the electrical control system can automatically start the pump motor, and constantly send water to the water tower, until the water level rises to a certain upper position, the control system can shut down the pump motor itself.
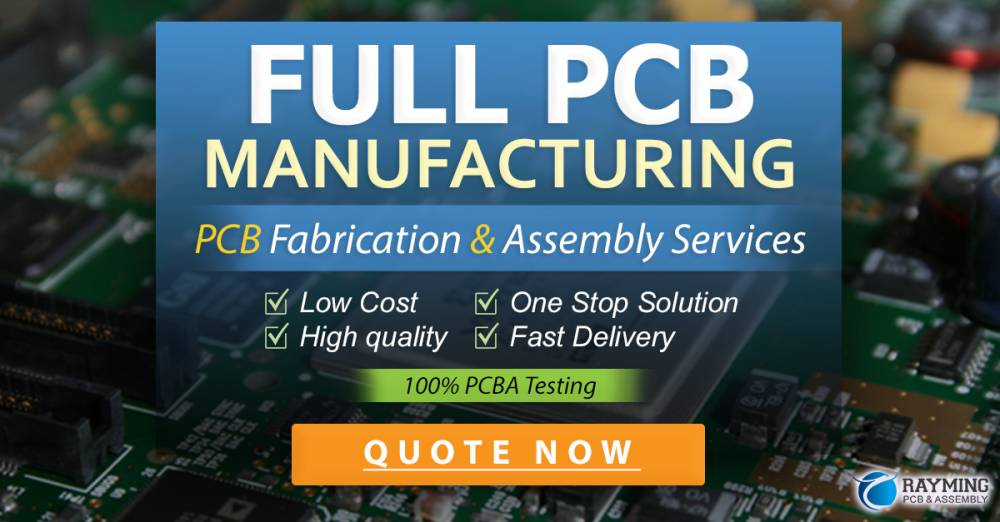
An automatic control system should also have the function of manual intervention, so that manual operation can be used when necessary to achieve the purpose of starting (or stopping) the pump motor at any time.
In addition, for the safety of the control system, there should be some necessary protection links – short-circuit protection and motor overload protection.
The control requirements and the realized line as shown in Figure 1 and 2.
The M in the schematic diagram is a pump motor (three-phase cage asynchronous motor), which is started and stopped by the opening and closing of the three main contacts of KM. KM is an AC contactor, and the closing and closing of its contacts are controlled by the solenoid coil of the contactor coil, and the right side of the schematic diagram is the control circuit of the contactor coil KM. The contactor will act, and the closing of the contacts will make the motor run; likewise, the control circuit is disconnected, and the contactor coil is disconnected and will make the motor stop.
According to the water tower control requirements, the motor should be started at the lower limit of the low water level (as shown in Figure 1), and then the motor is started through the water level monitoring system (the position shown in the float). The float 1 is in the lower limit position and the bump 2 is near the travel switch SQ2, so that the travel switch SQ2 is pressurized and the pair of normally open contacts of SQ2 is turned on, which makes the KM in the control circuit get power to operate, and the three normally open main contacts of KM in the main circuit are closed, and the motor M starts to run. As the pump works, the water level in the water tower gradually rises, the float rises and makes the bump down to leave the travel switch SQ2, the travel switch will be reset once it is not under pressure, thus making SQ2 normally open contacts open, if the control circuit is only controlled by SQ2 normally open contacts, then KM will be disconnected, making M stop, and the water level of the water tower is far from the upper limit level at this time, in order to solve this contradiction, as long as the To solve this contradiction, just connect a normally open contact of KM contactor in parallel next to the normally open contact of lower limit travel switch SQ2 in the control schematic. When SQ2 is connected to the KM circuit, the main contact of KM closes at the same time, a pair of normally open contacts in parallel with SQ2 also closes, and when the ram leaves SQ2 and makes SQ2I normally open disconnection, KM coil will not lose power, but continue to maintain the powered state, the contactor’s own action to maintain its powered state is called self-preservation (or self-locking), the normally open contact is called self-preservation (or self-locking) contact.
When the water level rises to the upper position, as the float rises and the block falls and SQ1 is pressurized, the normally closed contact will be disconnected, thus cutting off the coil circuit of KM and stopping the pump motor with the loss of power of KM (of course, the self-locking contact is also reset). When the water supply system makes the water level fall, the bumping block will rise and make SQ1 reset, and the coil KM will not get power at this time. Only when the water level drops to the lower water level will the motor start again.
How to intervene manually? For example, if you know in advance that there is going to be a power failure, in order to make the water tower water supply uninterrupted and full of water in advance, you should be able to start the pump motor when the water level is not at the lower limit, you can use the normally open contact of the manual button SB2 in parallel with the normally open contact of the lower limit travel switch SQ2, when needed, as long as you press the start button SB2, it can play the role of connecting the KM circuit instead of SQ2. For example, if the pump motor needs to be temporarily stopped due to maintenance, the stop button SB1 can be pressed to disconnect the normally closed contact and stop the motor.
Since the AC contactor does not have the function of short-circuit protection and overload protection, the control system additionally adds protection components – fuse and thermal relay. Fuse shortener FU1 (a group of three) quickly fuses when a short circuit occurs in the main circuit and electrical appliances behind it, and fuse FU2 (a group of two, or only one can be used), quickly fuses when a short circuit occurs in various parts of the control circuit to protect the supply power and electrical appliances from damage.
This control circuit has the following characteristics.
① water tower can be unattended, by the automatic control system according to the requirements of their own work.
②The key to the automatic control system is the detection of the water level and the relative position of the upper and lower limit travel switches and bumpers set, the principle is: the lower limit must be on, the upper limit off.
③To achieve the water level detection and control devices, switches, should be selected according to the specific circumstances of the site and the type of devices and switches available.
④ Both automatic control function and manual control. This is to meet the actual needs of the control, to remember the actual needs and ease of use is the highest pursuit of the control system.
⑤ For the two control modes of the motor, two start signals (normally open contacts) are used in parallel and two stop signals (normally closed contacts) are connected in series when realized on the schematic diagram.