The measurement of electrical power is essential for monitoring, analysis and control systems in any process. To perform these types of measurements, current sensors must be used. Physical quantities cannot be managed unless they can be measured. Let’s take an in-depth look at the behavior of current sensors.
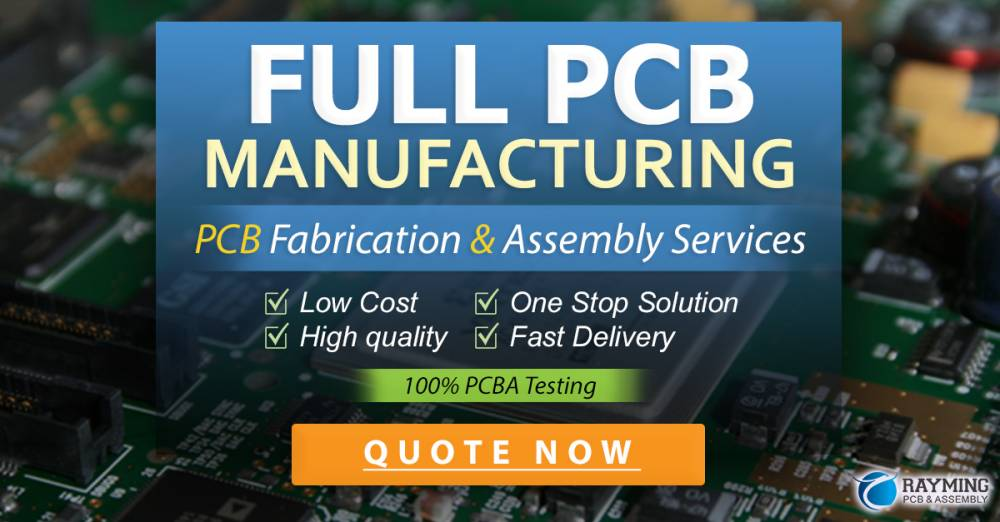
Current sensors
A current sensor is a device that converts a current signal into another signal that can be analyzed. The signal to be measured is called the “primary current” and the output signal is called the “secondary current or voltage”. The last signal is the one used in electronic boards, ADCs and other analog instruments. Because different measurement techniques exist and primary currents can vary depending on waveform, pulse type, isolation and current strength, the market offers a wide range of current sensors. As shown in Figure 1, the most common types of current sensors fall into two categories.
The first category applies Ohm’s Law ( V = R × I ) based on the operating principle of a “shunt”.
The second type uses Ampere’s law (I = # H × ds) and uses a magnetic field to measure current.

Ohm’s law applies to shunt measurements with the equation V = R × I. In practice, shunts are robust resistors with known ohmic values. When a current passes through a shunt, the resulting voltage is proportional to that current. Using this principle, we can obtain accurate AC and DC currents for less high currents. On the other hand, when the current rises and exceeds 100 A, too much heat is generated and the measurement system can become ineffective and critical.
Hall effect current sensors can be used to overcome these limitations. Powering a Hall probe applies a magnetic field perpendicular to the surface and produces a voltage proportional to the strength of the field. Ampere’s law can then be used to calculate the amount of current flowing through the conductor. Hall current sensors use a magnetic core to concentrate the magnetic field in the air gap where the probe is located. The output voltage is proportional to the magnetic field, which in turn is proportional to the primary current. The performance of the current sensor depends on the performance of the open-loop Hall probe. To improve linearity and reduce the drift of the temperature offset, the closed circuit principle is implemented and another type of current sensor is represented by a magnetoresistor, where the value of the resistor varies proportionally to the magnetic field. These current sensors are usually more accurate than Hall effect, but have sensitivity limitations due to the air gap. However, the device must ensure efficient and accurate measurements with very high detection quality, an extremely flat frequency response and excellent DC stability. All of these characteristics can be found in Danisense’s current sensors, and the company offers customized solutions to meet the exact needs of its customers.
Current Measurement Methods
Current measurements can be performed using the LT6106 integrated circuit, a versatile amplifier for current sensing (see the application diagram in Figure 2). Its features are highly regarded.
Maximum voltage offset: 250 µV
Maximum input bias current: 40 nA
Only two resistors are required to set the gain of the device
Accuracy: 1%
Maximum output current: 1 mA
PSRR: 106 dB
Its main applications are automotive and industrial, battery monitoring, energy management, engine control, lamp monitoring, and overcurrent and fault detection. The device measures current by detecting the voltage across an external resistor (shunt resistor). Internal circuitry converts this voltage to output current. the LT6106’s very low supply current also makes it suitable for battery applications.
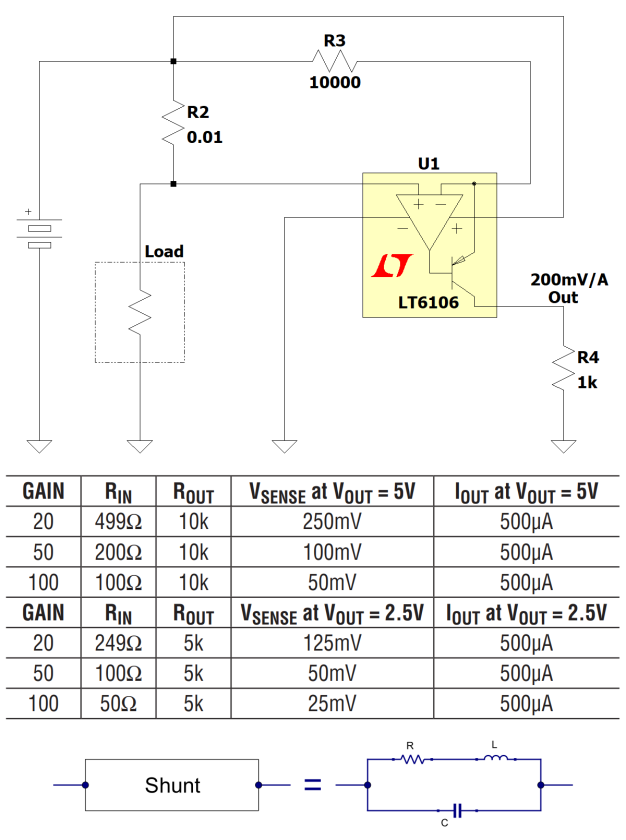
Once you understand how it works, you can easily configure the design to meet all your needs using Ohm’s Law and the power equation. In the example wiring diagram configuration, the power supply is 30 V and supplies a 19-Ω load at approximately 1.57 A. The 0.01-Ω shunt resistor does not affect the operation of the system, which consumes approximately 25 mW . Configure the configuration resistor to give the amplifier a unit of gain. In this case, the output voltage (absolute value) is equal to the current flowing through the load. The combined efficiency is very high, certainly exceeding 99.8%. Obviously, this solution cannot be used for very high currents.
Use of current sensors instead of shunts
Using a current sensor instead of a shunt has great advantages. A shunt, in fact, is not an ideal component, but as you can see from the previous wiring diagram, it has an inductive element (in series) and a capacitive element (in parallel). Therefore, it is necessary to measure current not only in DC but also in AC, so a more efficient method needs to be used to make better estimates in different frequency and current ranges to obtain a higher accuracy of the results.
Current sensors have the advantage of galvanically isolating the primary circuit from the secondary circuit. This eliminates interference from common mode voltage ripple and greatly reduces noise on the primary current. The output signal of the current sensor is higher and less noisy than that of a shunt. The much lower insertion impedance reduces power consumption and undoubtedly improves the short and long-term stability of the system.
A simple example illustrates the idea: the power consumption of a shunt resistor used to deliver 50 mV at 1,500 A is 75 W. In fact, its impedance is 0.000033 Ω. To achieve high measurement stability and repeatability, the shunt needs a very low temperature coefficient. The sensitivity in volts/ampere will vary if the system is used at low or high currents. For example, the DL2000UB-10V current sensor has an effective insertion impedance of less than 0.5 µΩ and an effective power consumption in the primary circuit of less than 1 W at 1,500 A, which is 100 times smaller than previous shunts. The signal-to-noise ratio is very high even with very low primary currents. The table in Figure 3, shows excerpts from the DS, DM, DL and DQ series of Danisense current sensors. These sensors are ultra-stable and highly accurate, and are based on a closed-loop operating principle that provides excellent linearity and stability over time.
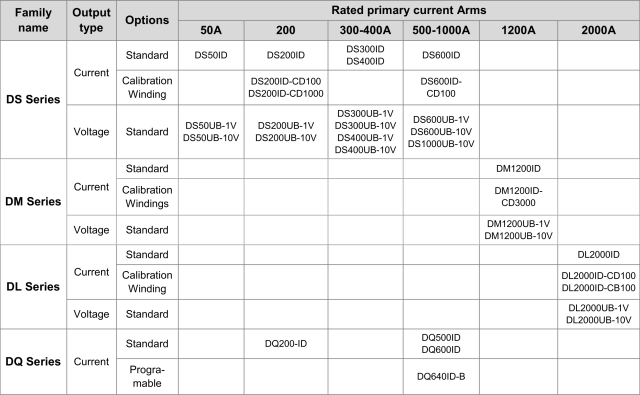
In a broad sense, certain models of transducer combinations can be classified as follows.
Transducers from 0 A to 600 A
DP50IP-B (72 A)
DC200IF (300 A)
DS400ID (600 A)
DS50UB-1V (150 A)
Sensors from 600 A to 3,000 A
DM1200ID (1,800 A)
DL2000ID (3,000 A)
DL2000ID-CB100 (3,000 A)
DL2000UB-10V (2,200 A)
Sensors greater than 3,000 A
DR5000IM (8,000 A)
DR10000IM (11,000 A)
DR5000UX-10 V/7,500 A (8,000 A)
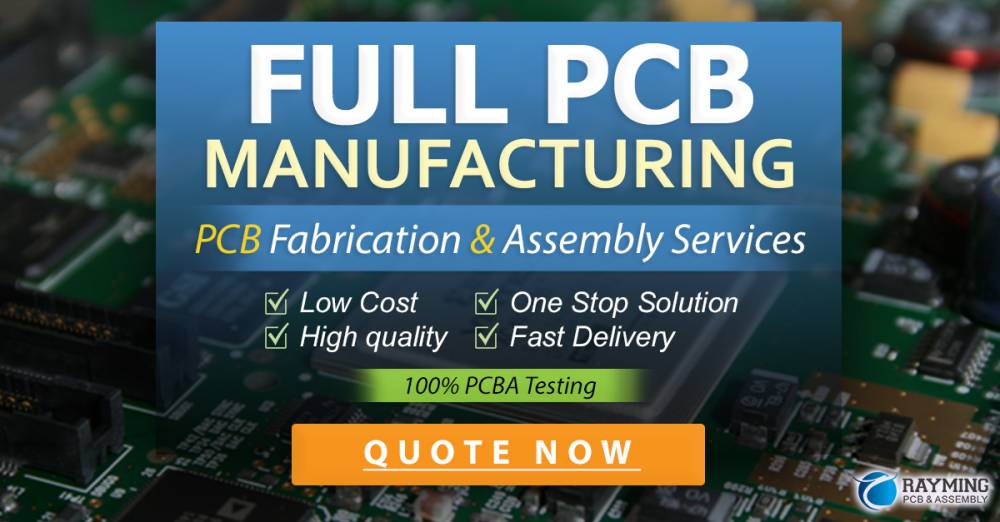
Some of these provide current output, while others provide voltage. One of the many interesting models is the DM1200UB-1V (Figure 4), an ultra-stable and highly accurate sensor for measuring non-intrusive and isolated DC and AC currents up to 1,800 A. The DM1200UB-1V has a 45 mm diameter opening. Its opening diameter is 45 mm, a width that allows for large insulated cables and the possibility of measuring leakage currents with high accuracy. With a linearity of 15 ppm and an offset of 10 ppm, its closed-loop technology allows for very precise measurements. The body is made entirely of aluminum for improved EMI shielding and a wide range of operating temperatures. Its applications range from power measurement and analysis to the construction of stable power supplies, from particle gas pedals to precision drives, from battery test and evaluation systems to power system calibration. The following are some of the electrical characteristics of the device.
Nominal primary AC current: max. 1,200 arms
Nominal primary DC current: max. 1,200 amps
Measurement range: from -1,800 A to 1,800 A
Nominal voltage output: -1 V to 1 V
Primary/secondary ratio: 0.8333 V/kA
Linearity error: from -15 ppm to 15 ppm
Bandwidth (3 dB): 400 kHz
Amplitude error (10 Hz to 3 kHz): 0.01
Amplitude error (3 kHz to 50 kHz): 1
Amplitude error (50 kHz to 300 kHz): 20
Supply voltage: ±14.25 V to ±15.75 V
Positive current consumption: 140 mA
Negative current consumption: 130 mA
Operating temperature range: -40˚C to 65˚C
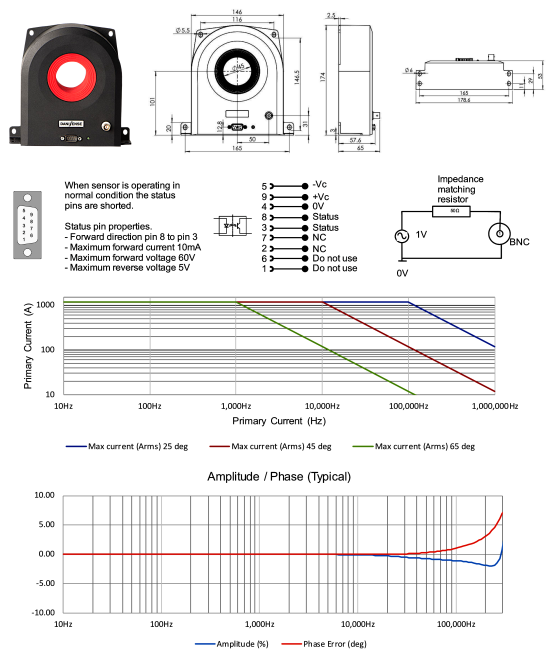
Conclusion
Today, all industrial systems have current sensors and in some cases, they are irreplaceable. Their main advantages are that they can be used and easily interpreted by industrial control systems and that they are completely isolated from the circuit and the load. In fact, it is not always convenient to connect the measurement system directly to the circuit in question. Their footprint is non-intrusive and they usually have a square or rectangular shape that may resemble a small speaker. However, their function is very important. The engineering behind the operation of the transducer is quite complex, but the analysis of its operation and output data is extremely simple, which is the most important aspect.