Foreword
The market segment with the best connector prospect is the automotive field. With the rapid development of the economy, the car has become one of the essential means of transportation for every household, so the future development of the car is particularly important for people’s lives. A wide range of market demand requires good product quality to ensure that this means that the automotive field used in the connector to be more stringent than other areas, to have excellent product quality but also good product performance to adapt and challenge the harsh use of the environment. So we design the connector is to take into account the stability and size and excellent functional stability.
The performance of unmodified PA66 materials cannot meet some specific requirements. This paper compares the performance changes before and after the modification of glass fiber reinforcement to find certain rules to guide the selection and design of connector products.
I. The effect of glass fiber reinforced PA66 on the moisture absorption properties of connectors
1.1 Glass fiber reinforced PA66
Any mechanical, physical, chemical and other effects to improve the original properties of nylon 66 can be called nylon 66 modification. The application of nylon 66 modification is also very wide, almost all nylon 66 resin properties can be improved through the modification method, such as appearance, aging resistance, wear resistance, flame retardancy and cost.
Glass fiber reinforced modification is a common way to physically modify plastic materials, after glass fiber reinforced PA66 materials, not only enhance the physical properties, but also can improve the stability of the products. However, the moisture absorption of nylon materials in the production is an inevitable problem, moisture absorption will not only affect the size of nylon products, but also affect the mechanical properties, thus affecting the function of the entire connector products. For the stability of the product, the need to verify the experiment, but also in the experimental process can also be through the process of data changes, to find some laws to know the design of the connection and product packaging, storage, transportation and other aspects, the experiment mainly compared 15%, 30%, 50% of three different glass fiber connector products, placed under constant temperature and humidity conditions, a group of natural placement of another group of samples immersed in water. Simulate the extreme conditions, and monitor the dimensional changes and performance changes of the two groups of samples according to the time change.
1.2 . Experimental method
1.2.1 Experimental materials
The experimental materials were provided by BASF (Shanghai) Trading Co.
1.2.2 Experimental equipment
The experiments were conducted by injection molding method to manufacture a standard part of the connector market, and the equipment used in the experiments is shown in Table 1.

1.2.3 Experimental operation
Three different glass fiber reinforced products of 15%, 30% and 50% were made, and each group of samples was divided into two, and one was placed in a constant temperature and humidity environment at 22℃ and 70% humidity; the other was immersed in pure water and left to stand in the same laboratory as the non-immersed product. After taking one sample of the unsubmerged product, subsequent samples were taken at 7, 14, 30 and 60 days, including both submerged and unsubmerged samples, to measure dimensional changes and changes in terminal pullout force.
The direction of glue feeding is defined as X direction and the direction perpendicular to the glue feeding is defined as Y direction as in Figure 1. The X- and Y-directional dimensions of each group of samples were measured using a digital microscope, and the statistical data were compared and analyzed.
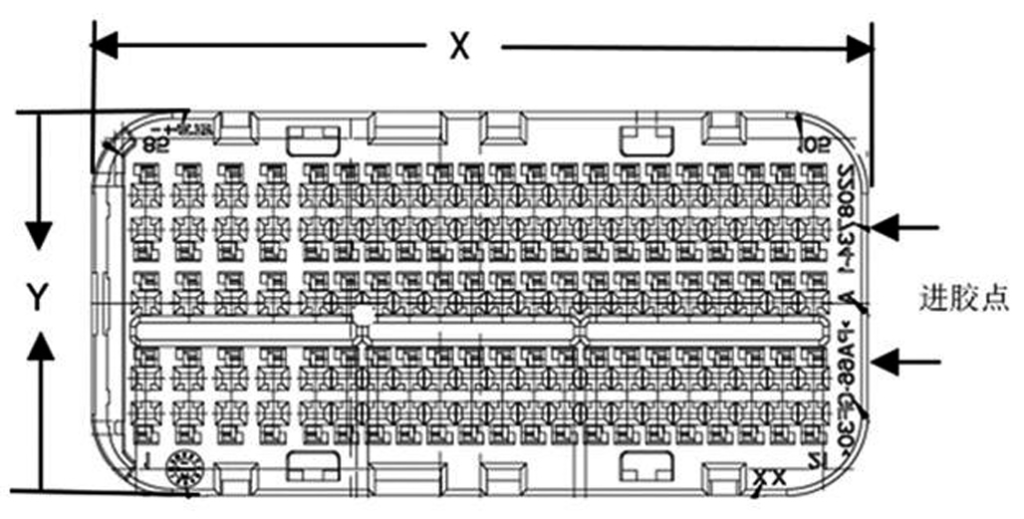
Fig. 1 Dimension posiTIon
Terminal pull-out force is an important manifestation of the connector performance, directly reflecting the connector function and durability performance. This experiment by using Tyco Electronics ( Suzhou ) company production of standard terminals, due to the terminal industry product tolerance of only 0.005mm, the experiment can be defaulted to the same batch of terminal size and performance no difference, so here do not discuss the terminal differences in this experiment. The terminal pull-out force is shown in Figure 2.

Fig. 2 Terminal pull out
1.3. Experimental results
By comparing the dimensional results, it is found that the X-direction dimension is relatively more stable than the Y-direction dimension. The value of the effect of water immersion is the ratio between the rate of change of the dimensions of the same group of products with and without water immersion for the same period of time, and this ratio is used to compare the overall level of change in the X and Y directions, as shown in the table.
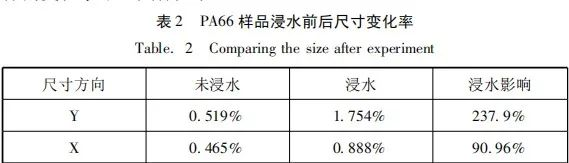
The Y direction is perpendicular to the direction of glue feeding, i.e., perpendicular to the direction of injection pressure, and the pressure received during the melt flow is relatively small compared with the X direction, and the gap between PA66 melt and glass fiber is relatively large. The size trend was found to be slowly increasing under natural conditions; under water immersion conditions, the size increased rapidly within 7 days, and then slowly increased, as shown in Figure 3.

Fig.3 Trend of change in size after experiment
From Fig. 4, it can be seen that the terminal pullout force of samples with different glass fiber contents under natural placement conditions showed a slow decreasing trend, and this trend started to decrease after the decrease on day 7 and the rebound on day 14. After the samples were immersed in water, there was a significant decrease on the 7th day, and the terminal pullout force of the immersed samples also started to rebound on the 14th day, but the rebound was not large. After the 14th day of water immersion, the terminal pullout force began to stabilize, and there was a slight but not obvious decrease.
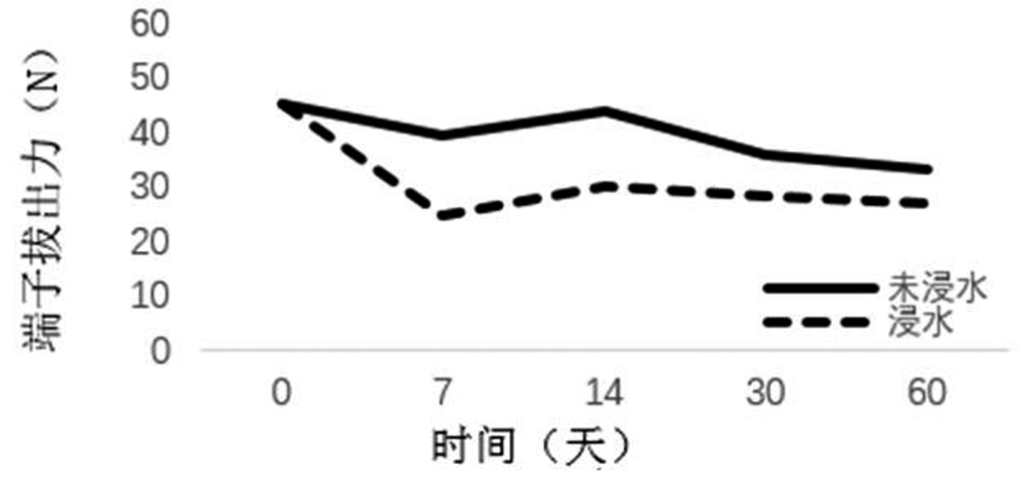
Fig.4Trend of change in pull-out strength after experiment
II Summary of the whole paper
( 1) The dimensional stability of PA66 material is poor. Whether it is placed naturally or under water immersion, its dimensional change is more obvious after water immersion, which accelerates its own process of water absorption. The dimensional change in the inlet direction is smaller than the other directions, and this feature can be referred to in the product design to design the key dimensions in the inlet direction.
( 2) The terminal retention force of PA66 material samples decreases on the 7th day whether it is placed naturally or immersed in water, only under the immersed condition, it is more obvious. It bounces back at day 14, and the subsequent all show a slow decreasing trend.
( 3) This experiment shows that the terminal retention force of PA66 material connectors will absorb moisture and decline with or without water immersion, only the time is different, and the higher the humidity, the faster the decline. To change this situation, it is necessary to change the environment in which the connector is located, such as sealing the packaging, adding desiccant, etc. The addition of these measures can extend the service life of PA66 material connectors.